JAIX WMS - Customer Setup
WMS - General
Jaix WMS > Customers > Main > Customers > [Customer Record] > WMS - General
Customer Level settings that apply for all Warehouses that the customer is enabled for.
General Settings
Enable WMS | Enables the Customer for use within WMS. Note that Customer will also need to be enabled for any Warehouses that they are to operate within under at Jaix WMS > Customers > Main > Customers > [Customer Record] > WMS - Warehouses |
Next Docket No. | A prefix can be added to Put and Pick Dockets at customer level. Prefixes set here will apply to all put and pick dockets for the customer for all Warehouses. Warehouse specific prefixes can be set at Customers > Main > Customers > [Customer Record] > WMS - Warehouses. Customer level Docket prefixes will override any global docket prefixes set in tools system setup. |
Pick Docket Settings
Setting | Refer Image | |
---|---|---|
Pick Docket Requires Service | 1 | Requires that a Freight Service is selected on a Pick Docket before the Docket can be saved. Services are setup within the Jaix Freight Application. |
Pick Docket Requires Carrier | 2 | Requires that a Carrier is selected on a Pick Docket before the Docket can be saved. |
Validate Docket Reference | 3 | Will check if the Pick Docket Reference already exists on another docket for this Customer and provide a Warning on Save of the docket. This is a warning only and will not prevent the reference from being used. |
Picked Status | 4 | When Pick Dockets are confirmed, either by scanning device or in the desktop application, dockets will be put into Picked Status. Products that are on Dockets that are in Picked status will still be charged storage until the docket is put into confirmed status. Dockets can be updated to confirmed status from within the opened docket, or in bulk from the docket search & list grid. Dockets cannot be updated from picked to confirmed using scanning devices. |
Pick Requires Reference to Confirm | 3 | Will disallow dockets from being confirmed without a docket reference being entered. Picked Status must be enabled to use this option. |
Disable Pick Auto Allocation | Disable the auto allocate button on the pick docket allocation screen. Auto allocate will allocate all docket items based on customer pick allocation priority settings. If pick allocation priority settings are not enabled, products will be allocated using first in first out rules. More information on custom pick allocation priority can be found below. |
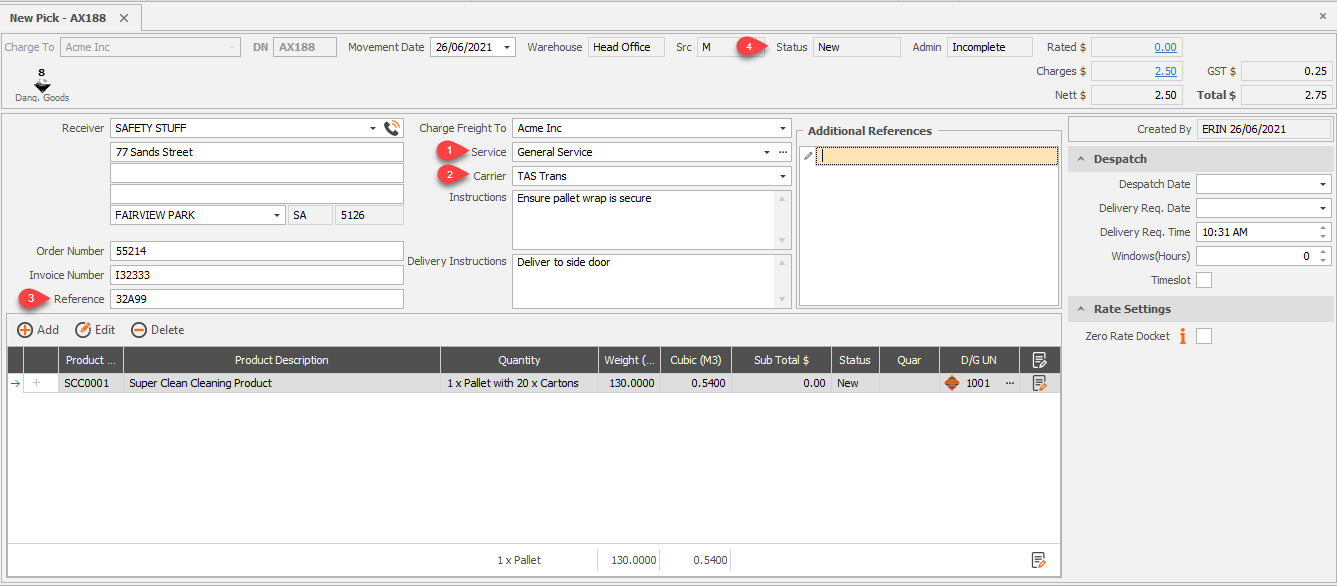
Put Docket Settings
Auto Quarantine incoming stock | All stock for the customer will be put under quarantine upon confirmation. For more information regarding quarantine functionality, please refer to JAIX WMS - Quarantine |
Put Docket Requires Service | Requires that a Freight Service is selected on a put docket before the Docket can be saved. Services are setup at Jaix Freight > Tools > System Setup > Freight Setup - General. |
Put Docket Requires Carrier | Requires that a Carrier is selected on a put docket before the Docket can be saved. |
Scanning Settings
Settings that effect some processes in the SmartSCAN WMS device application.
Require GTIN per Quantity Scanning | When picking, users will be required to scan the product GTIN for the count of picks. e.g. If the pick is for 5 items then the GTIN will need to be scanned 5 times. Where the license plate quantity is fully depleted, only a single GTIN scan will be required. |
Allow Serial Extract Scanning | Enables the ability to extract serial numbers from barcodes with combined part numbers and serial where specific conditions are met. |
Enforce Unique Serial on Inwards | Where products are enabled for serial numbers, and no serial has been recorded against a license plate, users will be prompted to scan or enter the serial on the SmartSCAN device. Enabling this options will disallow adding a serial that is not unique for the Customer. |
Substitution
When picking dockets using SmartSCAN, if the allocated product cannot be found users can long press on the item detail on the device screen to view a list of other available stock that could be picked instead. E.g. If there are multiple pallets of a product stored in a bulk stack location, and the allocated pallet is at the back, and not accessible, the allocated pallet could be substituted for one that is at the front and easily accessible. The below options control which pallets would be allowed to be substituted based on batch numbers, serial numbers and date requirement dates for the products. Where products have multiple options enabled, all three options will be checked.
Allow Different Batch | Will allow users to substitute any pallet of the same product, regardless of the batch number recorded. |
Allow Different Serial Numbers | Will allow users to substitute any pallet of the same product, regardless of the serial number recorded. |
Allow Different Date Requirement | Will allow users to substitute any pallet of the same product, regardless of the date recorded. |
GS1 Settings
For more information on SSCC please refer to JAIX WMS - Serial Shipping Container Codes (SSCC) in WMS
Enable SSCC | Check to enable SSCC for a Customer. If SSCC is enabled, and Generate SSCC on Inwards is disabled, labels will be generated on Outwards (Pick) Dockets only. |
Generate SSCC on Inwards | Enable to have an SSCC generated for all Docket Items on Inwards movements. SSCC numbers will be generated using the Next SSCC No. values specified on the Customer Record. |
Next SSCC No. | Enter the Customer's GS1 Assigned SSCC Prefix in to the first field. The Suffix will auto increment. |
Product Groups
Customer level reporting groups that are assigned to products. Product groups can be set to be excluded from EDI Response files. Product group is a mandatory field for products. If Product Groups are not required for internal or customer processes, it is recommended to set up a generic group such as default or storage.
Product groups are available in some report and form datasets and filters
They can also be useful for filtering in the product quick settings screen. For more info on product quick settings, please refer to Quick Settings to allow bulk edit of Product Setup
Custom Pick Allocation Priority
When allocating pick dockets, stock on hand is displayed in order of pick allocation priority settings. If Custom pick allocation priority is not enabled, first in first out (FIFO) ordering will be used. When using Custom priorities, multiple can be used together, and the orange arrows can be used to order the priorities. So for example, with the below priority setup we would look at all stock held in bulk stack and find anything that is not a full pallet. If there are more than one LPN that are not full pallets, the first one to be received into stock would be prioritised. Stock is then displayed in order of priority in the pick docket allocations screen, and allocated out using this order when using the allocate all button. This allocation order would also apply when orders are allocated during EDI docket creation or where auto allocate is enabled for dockets created via the WMS online Portal
All storage types, both system standard and custom (e.g. High Rack, Bulk Stack) are available in priorities as well as the below options.
Storage Type (High Rack, Bulk Stack etc.) | Will prioritise stock located in the storage type selected |
FIFO | First in First Out by product received date |
Least Remaining Qty First | LPN with the smallest base quantity. Note that where multiple config sets are on hand of a single product, config sets that have a smaller base quantity would be prioritised. Base quantity is the number of base units, hence the system will look at how many of the smallest item in the config set. |
Date Requirement Oldest First | Uses the oldest date recorded for date requirement date |
Part Handling Quantity | Uses LPNs where the Avl qty is not equal to a full pallet as per the product config set. e.g. if a pallet normally holds 50 cartons, but there is a pallet with only 40 cartons left on it, this would be prioritised over a full pallet of 50 |
Customer Default Print & Template Settings
Forms that can be printed from dockets can be customised at customer level. Select the form template for each document type to be used for this customer. Setting to Use default form, will use the branch level default. Setting to use Standard form, will use the Jaix standard form
Enabling the checkbox next to a form or label will have that document print as default when selecting Print > Customer Defaults from a docket, or when print is enabled for dockets created via EDI import.
Documents will print to printers as setup in WMS > Tools> Setup > User Setup.
Report Templates
Select the Charge Reports that should be attached to the Invoice during invoice process.
Charge Summary is the Charge Summary PDF, or custom reports created from it.
Charge Summary CSV will show Charge Summary CSV by Product, Charge Summary CSV License plate Breakdown and the Charge Summary CSV Detailed Report
The Charge Summary CSV by Product, and the Charge Summary CSV License Plate Breakdown reports only works where stock is put and picked as single items. Products must only have a single unit in the config set, and must never have a quantity greater than 1 entered on dockets. Where products have more than one unit in the config set, and dockets have quantities greater than one the Charge Summary CSV Detailed Report, or a custom report based on this should be used.
Reference Names
Reference names provide the ability to define 10 Customer specific product fields. The field labels are defined here on the customer record, and are available for the customer when setting up new products. For more information regarding Product setup, please refer to JAIX WMS - Product Setup
Product References on the Product Record
WMS - Warehouses
Settings under the Warehouse menu apply only to the Site selected.
Site
Site selection that all of the below settings apply to.
General
Enable Warehouse | Enables the Customer for use within the selected Warehouse. If the Customer is not enabled the will show in selections - e.g. unable to create a docket, see products, run reports etc. |
Primary Site | Where a Customer is enabled for multiple warehouses and dockets are created via WMS Portal without a site selected, the dockets will be created into the site enabled as the Primary Site. For more information please refer to Portal and Multiple Warehouse Site Management |
Docket Settings
Next Docket Number | Ability to define a Docket prefix to be used for the Customer for the selected Site. This would override any Customer level (set at Customer Record > WMS - General) or Global level (tools> System Setup) Prefixes |
Default Sender | Automatically populates the selected senders' details into put dockets, but can be edited on the docket if required. |
Default Receiver | Automatically populates the selected receivers' details into pick dockets, but can be edited on the docket if required. |
Req Unique Order Number | Ability to check that the docket order number is unique for the Customer. Option to show a warning, disallow or not validate at all. Will only validate if an order number is entered. Blank order numbers are allowed without validation. |
Pick Allocation Substitution
Settings apply to pick docket allocation.
Where a date, batch or serial has been specified on the pick docket, enabling this will enforce that the specified serial is allocated to the order. There is a user role setting in Jaix Admin that allows users to override this restriction.
Specifying details on pick dockets takes place in the Stock Details window that opens from Add or Edit on the Main Screen of dockets or via EDI / Web Portal.
Put Consignment Settings
Consignments or Jobs can be created from WMS dockets. Please refer to JAIX WMS - Ex WH Deliveries for more information.
Pick Consignment Settings
Put / Pick Consignment Settings | |
---|---|
Create into Freight | Select Freight, Jobs or None to determine the record type created into Freight from WMS Dockets |
Use Measure Quantity for CN Item Qty | When a Consignment / Job is created for measured products the Consignment detail line Item field will be set to the Measure Quantity (eg. Quantity in Metres) |
Create PUP | Enable to Create a Pickup as well as the above specified record |
For Local Only | If create PUP is enabled, will only create a Pick Up if the job is local. |
Use Docket No as Consignment No | Uses the WMS Docket number for the CN/Job number |
Requires Despatch Date | Despatch Date must be set in WMS for a CN / Job to be created |
Auto Validate Consignments | Consignments will be automatically Validated (rated) upon creation in Freight |
Set CN Sender Ref. to Docket Order Number | The WMS Docket Order Number will be populated into the CN / Job Sender Reference field |
Set CN Receiver Ref. to Docket Invoice Number | The WMS Docket Invoice Number will be populated into the CN/Job Receiver Reference field |
Set CN Details Ref as Serial | Sets the Detail Ref on the CN to the Serial Number listed for a Product if available |
Default Consignment Receiver / Sender | Select the Receiver or Sender to be used as Default on CNs/Jobs created from WMS |
Default Charge To | If the CN is not to be charged to the WMS Docket Charge to Account by default, a different Debtor can be selected here |
Put / Pick Consignment Detail Settings | |
Set CN Detail Ref as Serial | Product Serial Numbers will be set into the CN / Job Detail Line 'Detail Ref' Field. |
Detail Grouping | Products with a like Freight Unit will be grouped into a single Detail CN Line. Where the above setting is enabled, and products are Serialised, a single line would still be created for each unique Serialised Product. See Ability to consolidate picked stock for Consignment creation for more information. |
WMS - Units of Measure
Customer specific settings and options relating to product setup and handling.
Customer Units
Customer Specific Units of Measure that can be used in Product setup. Units defined here will only show for this customer. For example, if this customer is the only customer in my Warehouse that stores Jugs, define the unit here so that it does not show for any other customer. For more information on Product Setup please refer to JAIX WMS - Product Setup
Handling Units
Handling Units need to be enabled for a Customer before they can be selected on Put Dockets. To enable, select the Unit that the Handling Unit Type applies to and enable the Handling Type. Please refer to JAIX WMS - Managing Handling Unit Types for more information regarding Handling Unit Types.
Minimum Leave Quantity
Where products use Measured Units we can opt to set a minimum leave quantity. For example, cabling that is picked by the metre is stored on a roll in the Warehouse. An order is received for 55 metres and is allocated from a roll that has 55.2 metres. The remaining 20 cm of cabling is not a usable qty, so rather than have the Warehouse dispose of the remaining 20cm, it can be sent out with the order. Please see Minimum Leave and Associated Rate for more information.
UOM to Freight Conversions
When creating ex-warehouse consignments, WMS Units can be converted to Freight Units as specified at Customer or Global level. This gives the ability to convert multiple WMS Units of Measure into a single Freight Unit Consignment Line for rating purposes. Please see Add a new Debtor level WMS UOM to Freight Unit conversion for more information.