JAIX WMS - Product Setup
Overview
This document is to provide detailed instructions on the creation of a new product in WMS. Throughout this document we will cover the mandatory fields, and interaction between the products, their unit of measure configuration sets and the different branches. This will not provide a standard operating procedure as each customer utilizes our software differently. That being said the information contained within will give you the tools to devise your own.
Branches
All products are held against a Debtor, and the product list is global. This means that any Warehouse activated for WMS will have access to all products linked to that Debtor if the Debtor is enabled for the Warehouse.
Jaix WMS > Customers > Main – Customers > [Customer Record] > WMS - General > Enable WMS
This setting enables the Debtor to be used within WMS. Note that the Debtor will also need to be enabled for the Warehouse(s) that they will be active in also.
Jaix WMS > Customers > Main – Customers > [Customer Record] > WMS - Warehouses
Site - Select the Site the Debtor is to operate in
Enable Warehouse - Enable the Debtor to operate within this Warehouse
Products will not show for a Debtor in Product S&L unless the Debtor is enabled for the Warehouse from which you have S&L opened.
Unit of Measure Configuration Set
The product configuration set provides details regarding which UOMs the product will be handled in, along with specific details regarding those UOMs. It is a record of how the physical stock is configured. E.g. A pallet has 20 cartons on it, that each contain 10 items. Configuration sets used to track/report, handle and charge stock movements within WMS.
The Unit list itself will populate as a combination of the Global Units and the Customer specific Units.
Jaix WMS > Tools > System Setup > Global – Units of Measure.
Item, Carton and Pallet are configured as default, however Custom Units can be added if required.
Jaix WMS > Customers > Main – Customers > [Customer Record] >WMS – Units of Measure > Customer Units
Where a unit is specific to a single Debtor, they can be set up on the customer record. Customer Specific units will only show for the relevant Debtor.
E.g. Only Debtor Acme Inc. holds the unit Jerry in the Warehouse, so it is added to their Customer Record rather than at Global level. When creating products for Debtors that are not Acme, the Unit 'Jerry' will not be available as an option - it will only be available when creating products for Acme Inc.
Configuration Set Setup on the Product Record
The first Primary Unit is the Base Unit. This is the smallest Unit of Measure that the warehouse will recognize. The second Primary Unit will have a Sub Unit set to the first Primary Unit and the Quantity value is the number of Base Units that are comprised to form the second Primary Unit.
The following are mandatory fields that must be populated prior to saving a Product UOM Configuration Set:
- Name
- Default Reporting Group
The example below denotes product setup of 36 Cartons containing 6 items each sitting on a Pallet.
Primary Unit | Unit name. E.g. Item, Carton, Pallet etc. |
Sub Unit | Unit that makes up the primary unit. E.g. Primary Unit of Carton, has sub unit of Items - there are items in the carton. |
Qty | Number of sub units combined to make primary unit. E.g. Number of Items in each Carton. |
Default Pick Unit | Primary Unit used by default for Pick Dockets. E.g. when specifying a quantity on the pick docket it will be in the selected unit. The above has Carton Primary Unit selected as default Pick unit, so I a pick docket is for Quantity 100, that means Pick 100 Cartons. If selected, the pick unit will be automatically populated on the Pick Docket when the product is selected. If no default Pick Unit is selected the Pick Unit of Measure will need to be selected on the docket each time the product is added to a Pick docket. |
Default Put Unit | Primary Unit used by default for Put Dockets. E.g. when specifying a quantity on the Put docket it will be in the selected unit. The above has Carton Primary Unit selected as default Put unit, so if a put docket is for Quantity 100, that means 100 Cartons. If selected, the Put unit will be automatically populated on the Put Docket when the product is selected. If no default Put Unit is selected the Put Unit of Measure will need to be selected on the docket each time the product is added to a Put docket. |
Default Handling Unit | The unit by which stock is stored and moved around the warehouse. The Handling Unit selected on Put Dockets is how Storage will be charged. If there is a rate set up for inwards or outwards movements that is set as default for, for the default Handling Unit, it will automatically be selected on Put/Pick Dockets. For More information about Rates please refer to JAIX WMS - Rates and Charges |
Default Reporting | Unit used by default when generating WMS reports. |
EDI In | Specifies the unit in which Products will be specified on incoming EDI Documents. E.g. Pick & Put Dockets. These quantities will be converted into the Pick / Put Unit specified on the EDI Profile. |
EDI Out | Specifies the unit in which Products will be specified on outgoing EDI Documents E.g. Response Files |
KG(s) | A weight can be recorded for each primary units. Product must have "Requires Weight" enabled on the product record. Weights entered against any unit will auto calculate / multiply for any larger unit, but are able to be edited. If a value already exists for the larger unit it would need to be set to zero to auto calculate again. Weight set up on product records will be populated into Put dockets, but can be overwritten at Docket level if required. These weights can also be populated into Consignments created from Warehouse Dockets. It is allowed to enable Weight on the product record without recording one in the config set, to allow for Weights to be recorded at the time of Putaway. |
Length(m) | Length, Width and Height in metres can be specified for each Unit within the configuration set. These metrics can auto calculate the Cubic for the unit is Cubic is at 0 before entering. Length, Width and Height will not auto calculate / multiple for other units in the config set. Requires Cubic must be enabled on the product record to enter these into the Configuration Set. |
Width(m) | |
Height(m) | |
Cubic | Cubic can be entered with or with out product dimensions being entered for each unit. It is allowed to enable Cubic on the Product Record without recording Cubin in the configuration set to allow for Cubic being recorded at the time of Putaway. |
Product Creation
Jaix WMS > Customers > Products – Find/Setup > Operations - New
The following are mandatory fields that must be populated prior to saving your new product:
- Customer Name
- Global Reporting Group
- Product Group
- Product Code
- Product Description
- Unit of Measure Configuration Set
Product
Customer | Select the Customer that this product belongs to |
Global Reporting Groups | Global reporting group is for internal product reporting across all Debtors |
Product Group | Product group is to group products at Debtor level for customer specific reporting. These groups are available in some report filters and datasets to enable more targeted reporting. |
Code | Alphanumeric code that must be unique for each product per Debtor. |
Description | A short description of the product |
Attribute | A free entry text field to store any relevant attributes up to 50 characters |
Options
Shelf Life | The shelf life of a product (in Days). This value can be used to calculate Minimum Life on Receipt (MLOR) requirements and assist in allocating products with sufficient remaining Shelf Life. For more info on MLOR please refer Jaix WMS-Minimum Life on Receipt. |
Base UOM Price | The price of the first / base unit in the UOM Configuration Sets. Currently only accessible on the Product Record and is not available in reporting. |
Batch No. Required | Enable this to force Batch Number entry within put dockets. When enabled users will not be unable to confirm a put docket without a Batch Number entered. Options are available to prioritise or restrict allocations to specified Batch Numbers on pick dockets when allocating via "Allocate All' button or auto allocations via EDI. |
Serial No. Required (Inwards) | Enable this to force Serial Number entry within put dockets. When enabled users will be unable to confirm a put docket without a Serial Number entered. Options are available to prioritise or restrict allocations to specified Serial Numbers on pick dockets when allocating via "Allocate All' button or auto allocations via EDI. |
Serial Number Required (Outwards) | Enable this to force Serial Number within Pt Dockets. This allows products that have a serial to be putaway without capturing a Serial, with the view to capture them at the time of picking. This can be useful in scenarios where Customers do not pick by Serial Number, but do need to know which Serial numbers went out with which order. |
Requires Weight | Adds the weight field within the UOM Configuration Set. These fields can be utilized and edited on Pick and Put Dockets and assist in Consignment / Job creation from WMS into Freight. |
Requires Cubic | Adds the Length, Width, Depth and Cubic fields with the UOM Configuration Set. These fields can be utilized and edited on Pick and Put Dockets and assist in Consignment / Job creation from WMS into Freight. |
Third Party Reference | Enables a free text entry reference field held at License Plate level. |
Put Instructions | Free text to 50 characters for instructions that will be displayed on SmartSCAN devices when putting the product away. |
Pick Instructions | Free text to 50 characters for instructions that will be displayed on SmartSCAN devices when picking the product. |
SLE Override
If SLE is being utilised within the Warehouse the options here will override any Global SLE setting to enable more accurate SLE reporting at Product Level. For more information on SLE please refer to Jaix WMS – Standard Location Equivalent document.
SLE Product Unit | Select base unit to be used for SLE calculations |
SLE Value | Select the SLE value your locations can hold |
Units Per SLE | The number of Units that make up SLE Value set |
SLE Divisible | SLE Divisible products are able to be housed in a lesser SLE location as the SOH is reduced. |
SLE Divisible Product> | |
As the SOH reduces the required SLE also reduces. i.e. If above stock were housed in a 2 SLE location, it could be moved to a 1 SLE location after being reduced by 50%. | |
SLE not Divisible Product> | |
As the SOH reduces the required SLE remains the same as the stock requires the full 2 SLE width to be housed. |
Form Templates
License Plate | Default License Plate form which will override the Form set at Debtor and global level |
Freight Label | Default Freight Label form which will override the Form set at Debtor and global level |
SSCC (GS1) | Default SSCC (GS1) form which will override the Form set at Debtor and global level |
Where form Templates are set at product level, these will override all Global, Debtor and Branch level settings
Site Options
Branch | Unique Site Options can be set against a single product for each WMS branch. |
Preferred Location | Lists all Warehouse locations for Branch selected. Jaix will allocate to this location when you click "Allocate to Preferred" within the allocations screen on Put Dockets |
Putaway Range | Products will be allocated to available locations within the Putaway Range defined within Warehouses > Directed Putaway > Putaway Ranges. Please refer to https://jaixsoftware.atlassian.net/wiki/spaces/JSHD/pages/4850679 for more information. |
Auto Replenish | NA – Future functionality |
Minimum Base Stock Quantity | NA – Future functionality |
Reorder Base Stock Quantity | NA – Future functionality |
Auto Confirm Full Picks | |
Enable Custom Pick Workflows | For SmartSCAN WMS. When enabled a product scanned from a Pick Docket will ask for the Next Location instead of confirming the pick straight away. Products can be moved as many times as required to fulfil the workflow requirements. This might be useful where processes need to happen to stock before it leaves the warehouse. e.g. Decanting Liquid from an IBC might require the IBC to be moved to a measuring area for the liquid to be dispensed before the pick is confirmed. This setting works well in conjunction with JAIX WMS - Measure Operations |
Auto Confirm Full Picks | Only available when Custom Workflows are enabled. When a Pick is to fully exhaust the quantity of a License Plate it will auto confirm upon scanning instead of asking for the next location. E.g. If decanting the pick qty of liquid from the IBC would render the IBC empty, and as such the whole IBC container is to be sent out, then it would not need to be moved to the measuring area, and the pick could be confirmed and moved to a staging area instead. |
Dangerous Goods
Dangerous Goods Label | The Icon that represents the Dangerous Good selected |
Dangerous Goods Code | Obsolete Dangerous Goods code. New products cannot be assigned a code manually but must select from the Dangerous Goods UN dropdown |
Dangerous Goods UN | ID number to identify which Dangerous Goods category this product falls under |
Product References
There are 10 reference fields held against a Product record. These reference fields are set at a Debtor level, and can be customized to your needs. To rename the reference fields please navigate to
Jaix WMS > Customers - Main > Customer Name > WMS – General
All products assigned to this customer will have those reference fields available which can be assigned values from within the Product record form.
GS1 and Date Requirements
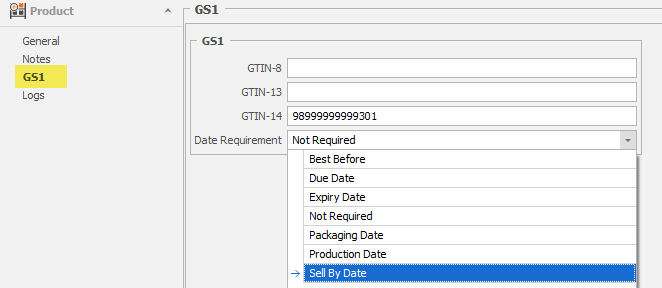
Where products are labelled with GS1 compliant GTINs these can be recorded against the product and utilised for SmartSCAN Scanning and SSCC label generation. Please consult the GS1 Australia website for more information regarding GS1 compliance and registration and JAIX WMS - Serial Shipping Container Codes (SSCC) in WMS for how these are utilised within Jaix WMS.
Date requirement types can also be set against a product. Where a date requirement type is set, Put Dockets will not be able to be confirmed unless a Date Requirement Date is entered for each handling unit. Date requirement dates can also be specified on pick dockets to be used in conjunction with auto allocation. e.g. If a date is specified for pick, when selecting 'Auto Allocate' on the pick docket allocations screen, or auto allocation takes place via EDI or Web Portal, only products of the correct date would be allocated (dependent on Customer record settings which can allow / disallow substitution)